Failure Analysis (Analisa Kegagalan) merupakan sutau tindakan yang dilakukan untuk menganalisa penyebab kerusakan secara detail pada peralatan dan perlengkapan instalasi pabrik. Beberapa jenis failure pada material yang sering ditemukan berupa retakan, patahan dan juga korosi.
Ada banyak faktor penyebab terjadinya kerusakan seperti pada saat proses perakitan, kesalahan dalam pengoperasian mesin atau alat, terjadinya kegagalan pada tahap manufacturing, dan lainnya. Dengan begitu dibutuhkan suatu tindakan deteksi kerusakan agar proses industri dapat berjalan dengan lancar.
Tujuan Analisa Kegagalan (Failure Analysis)
Tujuan utama dari failure analysis adalah mendeteksi indikasi kerusakan pada setiap material ataupun peralatan industri agar tidak terjadi kerusakan yang lebih besar lagi dan kerusakan tersebut tidak terulang kembali.
Dalam menganalisa kegagalan setidaknya ada 7 metode dasar yang dilakukan, yaitu :
1. Pengamatan visual
2. Analisa Identifikasi
3. Analisa tekanan
4. Microtoming
5. Uji Mekanik
6. Thermal Analytic
7. Teknik Nondestructive Testing (NDT)
Suatu komponen atau material dinyatakan gagal apabila :
Komponen atau material tersebut sudah tidak bisa digunakan atau berhenti beroperasi sama sekali
Komponen atau material masih bisa digunakan tapi masa pemakaiannya tidak terlalu lama
Komponen atau material tersebut mengalami gangguan sehingga jika digunakan atau dinyalakan malah membahayakan.
Ciri atau tanda awal suatu komponen mengalami kegagalan adalah timbulnya retakan dan patahn yang menjalar ke beberapa bagian sehingga menyebabkan cacat material. Berikut ini jenis-jenis patahan dan retakan :
Patah Ulet (Ductile fracture)
Patah ulet disebabkan beban statis pada komponen atau material. Jika beban tersebut dihilangkan maka rambatan patahan akan berhenti. Kondisi patah ulet biasanya ditandai dengan deformasi plastis yang besar di area patahan sehingga bagian permukaan yang patah akan terlihat kasar, berserabut dan berwarna kelabu.
Patah Getas (Brittle fracture)
Patah getas ini memiliki ciri rambatan retak yanga lebih cepat jika dibandingkan dengan retak akibat patah ulet. Selain itu, bisa dibilang hampir tidak ada deformasi plastis karena penyerapan energinya sangat sedikit.
Ciri lainnya, permukaan pada patahan komponen atau material terlihat lebih mengkilap dan rata sehingga bisa dilihat dengan jelas secara kasat mata.
Jenis patah getas dilihat berdasarkan batas butir. Jika batas butirnya diikuti bidang patahan pada material mengikuti batas butir disebut getas intergranulas. Namun, jika patahannya memotong batas butir maka disebut patah getas transgranular.
Patah Lelah (Fatigue fracture)
Kondisi patah Lelah dapat terjadi ketika suatu konstruksi menerima beban yang berulang walaupun harga tegangan nominalnya dibawah kekuatan luluh material.
Ketika komponen struktur mengalami pemusatan tegangan (stress concentration) yaitu suatu kondisi ketika tegangan di lokasi struktur melewati batas luluh material sehingga terjadi deformasi plastis dalam skala makroskopis.
Dari lokasi terjadinya pemusatan tegangan maka akan muncul retakan Lelah (crack initiation) dan terus mengalami perambatan retak (Crack Propagation).
Jika retak Lelah ini terus merambat jauh hingga bagian luas penampang tidak dapat menampung beban maka komponen akan mengalami patah. Kondisi ini disebut patah akhir (Final Fracture).
Retak Korosi Tegangan (Stess corrosion cracking)
Keretakan ini terjadi pada bagian komponen atau material struktur yang sudah mengalami karat. Secara definisi, retak korosi tegangan merupakan kombinasi tegangan tarik yang dipengaruhi lingukungan yang memiliki kandungan ion ataupun larutan kimia.
Retakan ini memang tidak dapat dilihat dengan jelas secara kasat mata maka dari itu dibutuhkan alat seperti mikroskop untuk menganalisa kerteakannya.
Mulur (Creep) dan Stress Rupture
Peristiwa mulur pada konstruksi terlihat dengan adanya deformasi plastis yang besar. Kondisi mulur ini bisa terjadi jika material berada pada suhu yang tinggi di atas 0,4 atau 0,5 derajat kelvin pada titik cair material yang digunakan.
Sedangkan kondisi stress rupture ditandai dengan adanya retak intergranular yang berada di sekitar lokasi patahan.
source: testindo.com
Ada banyak faktor penyebab terjadinya kerusakan seperti pada saat proses perakitan, kesalahan dalam pengoperasian mesin atau alat, terjadinya kegagalan pada tahap manufacturing, dan lainnya. Dengan begitu dibutuhkan suatu tindakan deteksi kerusakan agar proses industri dapat berjalan dengan lancar.
Tujuan Analisa Kegagalan (Failure Analysis)
Tujuan utama dari failure analysis adalah mendeteksi indikasi kerusakan pada setiap material ataupun peralatan industri agar tidak terjadi kerusakan yang lebih besar lagi dan kerusakan tersebut tidak terulang kembali.
Dalam menganalisa kegagalan setidaknya ada 7 metode dasar yang dilakukan, yaitu :
1. Pengamatan visual
2. Analisa Identifikasi
3. Analisa tekanan
4. Microtoming
5. Uji Mekanik
6. Thermal Analytic
7. Teknik Nondestructive Testing (NDT)
Suatu komponen atau material dinyatakan gagal apabila :
Komponen atau material tersebut sudah tidak bisa digunakan atau berhenti beroperasi sama sekali
Komponen atau material masih bisa digunakan tapi masa pemakaiannya tidak terlalu lama
Komponen atau material tersebut mengalami gangguan sehingga jika digunakan atau dinyalakan malah membahayakan.
Ciri atau tanda awal suatu komponen mengalami kegagalan adalah timbulnya retakan dan patahn yang menjalar ke beberapa bagian sehingga menyebabkan cacat material. Berikut ini jenis-jenis patahan dan retakan :
Patah Ulet (Ductile fracture)

Patah ulet disebabkan beban statis pada komponen atau material. Jika beban tersebut dihilangkan maka rambatan patahan akan berhenti. Kondisi patah ulet biasanya ditandai dengan deformasi plastis yang besar di area patahan sehingga bagian permukaan yang patah akan terlihat kasar, berserabut dan berwarna kelabu.
Patah Getas (Brittle fracture)
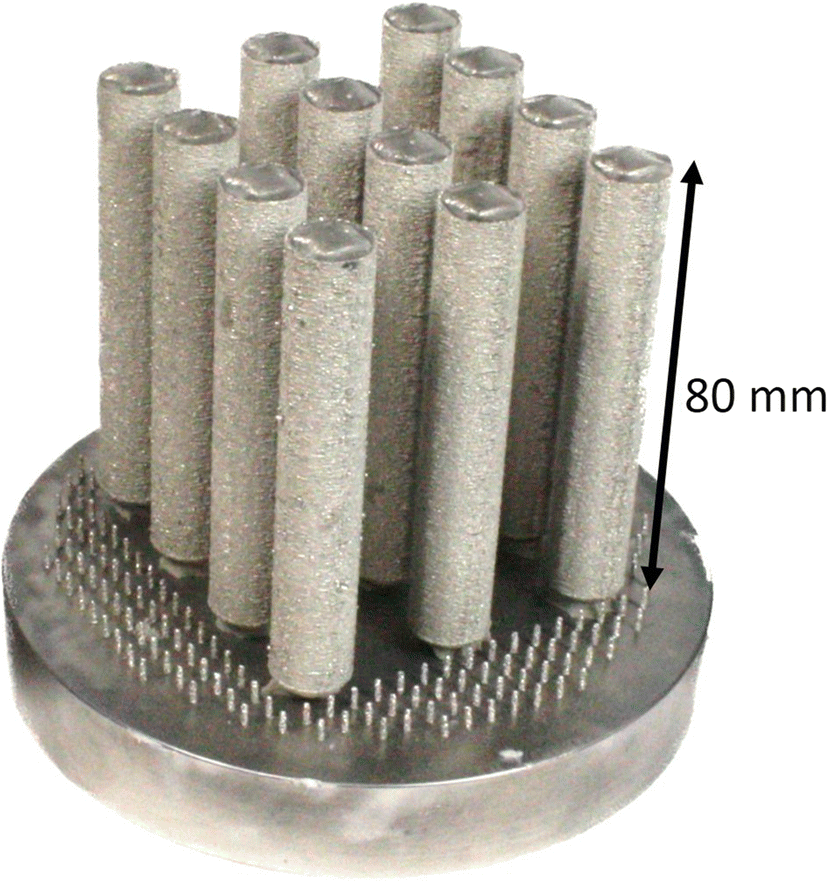
Patah getas ini memiliki ciri rambatan retak yanga lebih cepat jika dibandingkan dengan retak akibat patah ulet. Selain itu, bisa dibilang hampir tidak ada deformasi plastis karena penyerapan energinya sangat sedikit.
Ciri lainnya, permukaan pada patahan komponen atau material terlihat lebih mengkilap dan rata sehingga bisa dilihat dengan jelas secara kasat mata.
Jenis patah getas dilihat berdasarkan batas butir. Jika batas butirnya diikuti bidang patahan pada material mengikuti batas butir disebut getas intergranulas. Namun, jika patahannya memotong batas butir maka disebut patah getas transgranular.
Patah Lelah (Fatigue fracture)

Kondisi patah Lelah dapat terjadi ketika suatu konstruksi menerima beban yang berulang walaupun harga tegangan nominalnya dibawah kekuatan luluh material.
Ketika komponen struktur mengalami pemusatan tegangan (stress concentration) yaitu suatu kondisi ketika tegangan di lokasi struktur melewati batas luluh material sehingga terjadi deformasi plastis dalam skala makroskopis.
Dari lokasi terjadinya pemusatan tegangan maka akan muncul retakan Lelah (crack initiation) dan terus mengalami perambatan retak (Crack Propagation).
Jika retak Lelah ini terus merambat jauh hingga bagian luas penampang tidak dapat menampung beban maka komponen akan mengalami patah. Kondisi ini disebut patah akhir (Final Fracture).
Retak Korosi Tegangan (Stess corrosion cracking)

Keretakan ini terjadi pada bagian komponen atau material struktur yang sudah mengalami karat. Secara definisi, retak korosi tegangan merupakan kombinasi tegangan tarik yang dipengaruhi lingukungan yang memiliki kandungan ion ataupun larutan kimia.
Retakan ini memang tidak dapat dilihat dengan jelas secara kasat mata maka dari itu dibutuhkan alat seperti mikroskop untuk menganalisa kerteakannya.
Mulur (Creep) dan Stress Rupture
Peristiwa mulur pada konstruksi terlihat dengan adanya deformasi plastis yang besar. Kondisi mulur ini bisa terjadi jika material berada pada suhu yang tinggi di atas 0,4 atau 0,5 derajat kelvin pada titik cair material yang digunakan.
Sedangkan kondisi stress rupture ditandai dengan adanya retak intergranular yang berada di sekitar lokasi patahan.
source: testindo.com